Back to Tool Changers
Case Study: Oxford Automotive (Canton, MS)
New innovation greatly reduces time and complexity for
tool changes in DeviceNet environments.
Problem:
Oxford Automotive, a Tier 1 automotive
supplier located in Canton, Mississippi, encountered some issues while
implementing a robotic cell containing Six-Axis industrial robots, ATI Quick
Change Tool Changers, and a DeviceNet network environment for tooling control.
In this cell, several industrial robots complete a variety of material handling
and welding operations, performing multiple tool changes during each and every
cycle. Each robotic end-effector has multiple I/O devices and sensors as a part
of its configuration.
Oxford’s goal was to keep cost, weight, cycle
time, and wiring to a minimum. The following were factors for this project:
-
DeviceNet physical layer
(trunkline-dropline) restrictions add design complication to ensure proper
termination at the tooling.
-
Standard DeviceNet modules on the tooling
were taking too long to come online during a tool change to meet cycle time
requirements.
-
Running discrete wires to each sensor and
actuator on the tool through the tool changer is not a viable option, as it is
ungainly and adds weight and complication to the tooling.
Oxford was experiencing delays of up to 8
seconds per tool change during a multi-change cycle when implementing current
DeviceNet technology. Due to the cycle frequency, this series of delays added
significant time to the process, to the point of being unacceptable for
production.
Oxford presented these issues to the Design
Engineers at ATI who responded with new, cutting-edge technology.
Solution:
The standard way of obtaining DeviceNet I/O
from robotic tooling is to pass DeviceNet signals through the tool changer to
the nodes on the tooling. With this method, each device on the tooling is a
node on the host network and is connected and disconnected with each tool
change cycle. As a result, using standard DeviceNet technology produces a delay
of up to 8 seconds before tool ID is achieved, adding costly delays to the
cycle.
With ATI InstaTool technology, the host
DeviceNet network ends at the tool changer master, which is connected to the
network at all times.
The tooling I/O is connected to specific
models of commercially available DeviceNet I/O blocks.
These DeviceNet I/O blocks are then connected via standard DeviceNet
wiring to the tool changer tool-side ATI InstaTool module. Since
the tooling I/O is accessed as if it were part of the tool
changer master DeviceNet node, connection delays are greatly reduced.
The tool communicates the I/O to the master with a non-DeviceNet industrial
communications protocol.
ATI has optimized the power-up sequence of
the tooling I/O devices, resulting in the tooling I/O being available to the
host network in less than 1 second -- all end-effector I/O is available on
DeviceNet by the time a tool couple operation is completed. No more waiting for
DeviceNet nodes to come up on the network.
DeviceNet -
with and without ATI InstaTool
The illustrations below indicate the
fundamental differences between standard DeviceNet connectivity and the new ATI
InstaTool technology.
Standard
Network
Before ATI InstaTool, the DeviceNet signal passed from the DeviceNet
controller, through the master side to the tool side of the tool changer, then
on to the nodes.
With this method, each time a new tool side connection is made, up
to an 8-second start-up delay occurs before tool identification is made and the
application can continue.
|
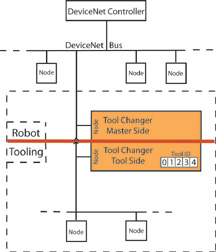
|
ATI Solution
With InstaTool, the DeviceNet signal effectively stops at the tool
changer master, creating an always-on connection to that master node. Using
patent-pending high-speed technology, the master node handles all I/O
communication downstream from the master.
The result is a connect time of less than 150 milliseconds for tool
ID and under 700 milliseconds for tool I/O. Tool I/O appears at the master
node.
|
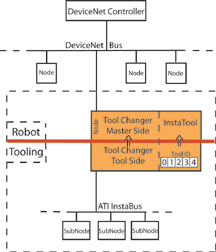
|
Results:
After implementation of ATI InstaTool, the
tool change delay has been completely eliminated. The robot moves, with tool
attached, immediately after the lock operation is completed. There has
been no observed latency on any of the control signals or sensor inputs.
Overall, Oxford is experiencing a dramatic improvement in efficiency and
productivity using InstaTool. All of the ATI Quick Change Tool Changers are
performing with the same high-level of performance as other ATI products.
Upon completion everyone
expressed their extreme satisfaction with the ATI InstaTool product.
Discussions were initiated about outfitting the entire plant with ATI InstaTool
changers.
Summary:
-
Easy to implement with new
cells or retrofit into existing cells
-
Simple, intuitive
configuration using DIP switches
-
Integrated diagnostics to aid
troubleshooting
-
Uses standard DeviceNet-type
cabling
-
Works with standard ATI Quick
Change Tool Changer models -
QC-151, 152, 201, 202, 303, 501, 502
Back to Tool Changers
|