Many robot companies such as ABB and KUKA are offering force control packages with ATI Force/Torque Sensors integrated into the robot. Forces and torques are measured by the sensor at the wrist of the robot giving it a sense of touch. Together, the robot and sensor make it possible to automate difficult assembly, machining, and finishing tasks that previously required skilled personnel or complex assembly machines.
Stäubli is the latest to join the group and recently announced that ATI's Net F/T Six-Axis Force/Torque Sensor System provides true plug-and-play connectivity via Ethernet to their CS8 robot controllers. The ATI Net F/T transducer with Net Box interfaces to a Stäubli robot controller via a TCP/IP socket and Stäubli's optional VAL3 library which reads force values.
The Net F/T Sensor System measures six components of force and torque (Fx, Fy, Fz, Tx, Ty, Tz) and is available with all of ATI's Force/Torque Transducer models. ATI's Six-Axis Force/Torque Sensors were designed to work with a variety of industrial robots; contact ATI for more information.
Product advantages include:
- Web-based configuration
- Cable-break detection
- Programmable thresholding
- Built-in status indicators
- Overload protection
- Temperature compensation
- High signal-to-noise ratio
- Tool transformations
- High-speed output
- LAN connectivity
More information on the Net F/T here.
More information on our Force/Torque Sensors here.
More information on ABB Robotics here.
More information on KUKA Robotics here.
More information on Stäubli Robotics here.
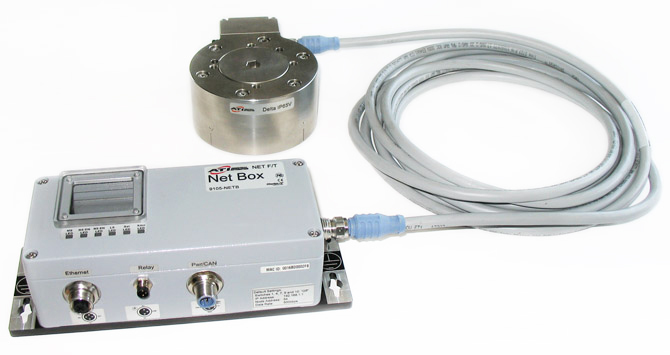
Net F/T System: Net Transducer, Cable, and Net Box