Big changes at ATI payoff with improved quality and faster delivery
Apex, NC,
January 9, 2008
ATI Industrial Automation's recent expansion and process improvements are already seeing positive results including shorter leads times and improved quality and on-time delivery.
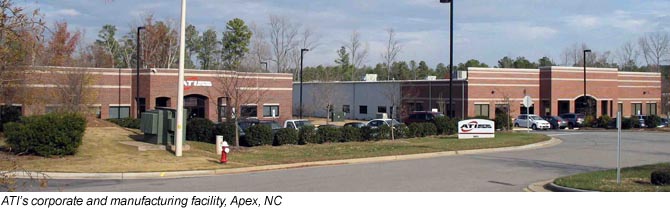
-
Construction of a second building at ATI’s corporate and manufacturing facility in Apex, NC has been completed. Doubling the size of its current facility, the additional space has created much-needed room for added engineering, manufacturing and inventory capacity, allowing ATI to quickly fulfill the high demand for its robotic end-effector products and Force/Torque Sensors.
-
A new office in the Detroit, MI area was opened. Conveniently located near I-75 and M-59 in the heart of "Automation Alley", the new office will enable ATI to provide even faster on-site sales and customer service to the many surrounding high-tech businesses.
-
A new office was opened in China. Located in the Xuanwu District of Beijing, the new office will allow ATI to provide service and sales support for all its robotic end-effector products to mainland China, Hong Kong and Taiwan.
-
A temperature controlled metrology lab was created to house precision measuring equipment including two CMMs (Coordinate Measuring Machines), providing consistent critical measurements down to .0004 of an inch.
-
A highly customized serial number tracking system was implemented for tracking products and components from the time they are built to when they are shipped. This system has improved customer service by enabling employees to see the entire history of a unit and its components simply by scanning its serial number. It has also aided in ATI's inventory accuracy by reducing data entry errors.
-
Customer service and communication was improved through a highly integrated information infrastructure and improved ERP (Enterprise Resource Planning) system implementation.
-
The additional space allowed the production workflow process to be reorganized for faster manufacturing and delivery.
-
An improved RMA system was developed for faster repairs, reducing customer downtime, and to track product problems in more detail, helping to improve quality.
-
A new Design Control process was implemented to help ensure that new product designs meet customer specifications, and to ensure that key dates are met during the design and build process.
-
The Safe Launch Initiative, a cross-functional team and process consisting of employees representing each department, was created to ensure quality and on-time delivery of newly-designed products.
-
New supplier corrective action processes were established to ensure that suppliers provide components that meet ATI's high-quality standards.
ATI Industrial Automation is the leading engineering-based world developer of robotic accessories and robot arm tooling, including Automatic Tool Changers, Multi-axis Force/Torque Sensing Systems, Robotic Deburring Tools, Robotic Collision Sensors, Rotary Joints, and Compliance Devices. Our robot end-effector products are found in thousands of successful applications around the world. Since 1982, our team of mechanical, electrical and software engineers, the largest of its kind for a robotic end-effector company, continues to develop new cost-effective, state-of-the-art end-effector products and solutions that improve robotic productivity.
|